thread galling pdf
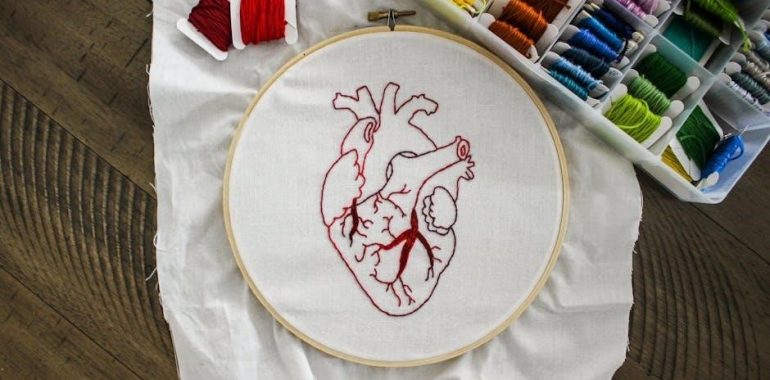
thread galling pdf
Thread galling is a form of abrasive wear caused by friction between sliding metal surfaces, particularly in threaded connections․ It occurs during assembly when bolts and nuts are tightened, especially with similar materials like stainless steel, leading to damage and difficulty in disassembly․ Understanding and addressing this issue is crucial for maintaining the integrity and longevity of mechanical components across various industries․
1․1 Definition of Thread Galling
Thread galling, also known as galling or cold welding, is a form of abrasive wear that occurs when two metal surfaces slide against each other under pressure․ It is particularly common in threaded connections, such as bolts and nuts, where friction and heat during assembly can cause microscopic metal fragments to transfer from one surface to another․ This phenomenon leads to the formation of a bond between the threads, resulting in damage to the components and difficulty in disassembly․ Understanding this definition is crucial for identifying and addressing the issue in various mechanical applications․
1․2 Importance of Understanding Thread Galling
Understanding thread galling is essential for preventing damage to threaded components and ensuring the reliability of mechanical systems․ When galling occurs, it can lead to costly repairs, downtime, and safety risks, particularly in critical applications․ Recognizing the causes and symptoms of galling enables the implementation of effective preventive measures, such as proper lubrication and controlled assembly techniques․ This knowledge is vital for maintaining the integrity of fasteners and ensuring smooth operation across industries like automotive, aerospace, and industrial manufacturing․ Addressing galling proactively saves time, reduces maintenance costs, and enhances overall system performance․
Causes of Thread Galling
Thread galling primarily arises from high pressure, friction, and heat during assembly, exacerbated by using similar materials and poor thread smoothness or cleanliness․
2․1 High Pressure and Friction
High pressure and friction are primary contributors to thread galling․ When bolts and nuts are tightened, extreme pressure forces metal asperities together, causing them to bond and seize․ This phenomenon, known as Cold Welding, is particularly prevalent in materials like stainless steel, which can fuse under stress․ Friction during assembly generates heat, softening the metal and increasing the likelihood of galling․ Additionally, high-speed power tools can exacerbate this issue by applying torque too quickly, intensifying friction and heat buildup․ Proper torque control and tool selection are essential to mitigate these risks and prevent galling․
2․2 Heat Generation During Assembly
Heat generated during assembly significantly contributes to thread galling․ Friction between threads causes metal surfaces to heat up, softening the material and increasing the likelihood of seizing․ This is particularly problematic with materials like stainless steel, which can gall more easily due to their properties․ High-speed assembly tools exacerbate heat buildup, further increasing the risk․ Managing assembly speed and using lubricants can help reduce temperature rises, preventing galling and ensuring smooth, secure connections․ Proper cooling techniques and tool control are also essential to mitigate this issue effectively․
2․3 Use of Similar Materials
The use of similar materials in threaded components significantly increases the risk of galling․ When both the bolt and nut are made from materials with comparable hardness and chemical properties, the likelihood of metal-to-metal bonding rises․ Stainless steel components, for instance, are particularly prone to galling when mated together due to their similar properties․ This phenomenon occurs because the materials’ surfaces can easily seize and weld together under pressure․ To mitigate this, mixing material grades or using components with differing hardness levels is recommended, as this reduces the tendency for the threads to gall during assembly or operation․
2․4 Thread Smoothness and Cleanliness
Thread smoothness and cleanliness play a critical role in preventing galling․ Rough or uneven thread surfaces increase friction, raising the likelihood of metal-to-metal bonding; Contaminants like dirt, grease, or debris can further exacerbate this issue by acting as abrasives․ Clean, smooth threads reduce friction and prevent the adhesion of metal particles, minimizing galling risks․ Regular inspection and maintenance of thread surfaces are essential․ Proper cleaning and deburring during manufacturing and assembly ensure optimal thread engagement and reduce the potential for galling․ Smoothness standards should be adhered to, especially in high-stress applications, to maintain component reliability and performance․
Effects of Thread Galling
Thread galling can severely damage threaded components, making disassembly difficult and potentially requiring costly repairs or replacements․ It also leads to increased maintenance costs and downtime․
3․1 Damage to Threaded Components
Thread galling causes significant damage to threaded components by transferring material from one surface to another, leading to surface abrasion and wear․ This can result in seized or frozen threads, making disassembly challenging․ The damage often occurs when similar materials, such as stainless steel, are used for bolts and nuts, as they are more prone to galling․ Over time, the threads can become stripped or deformed, rendering the components unusable․ In severe cases, this damage may necessitate the replacement of entire parts, adding to maintenance and repair costs․
3․2 Difficulty in Disassembly
Thread galling often results in significant difficulty during disassembly, as the seized threads can make it challenging to separate components․ This issue arises when material transfer between surfaces creates a strong bond, effectively locking the parts together․ Attempting to force the components apart can lead to further damage, such as stripped threads or broken bolts․ In severe cases, specialized tools or methods may be required to remove the damaged fasteners, adding time and effort to maintenance tasks․ This difficulty can also increase the risk of damaging surrounding equipment or structures during disassembly․
3․3 Increased Maintenance Costs
Thread galling significantly increases maintenance costs by requiring additional time, tools, and materials to address damaged components․ When threads are seized, disassembly becomes labor-intensive, often necessitating specialized tools or even the replacement of entire parts․ This extends downtime and raises expenses for repairs, particularly in industries where equipment availability is critical․ Additionally, the need for frequent inspections and premature replacement of galled components further escalates operational costs, making thread galling a costly issue to resolve and maintain․
Preventive Measures
Lubricating threads, reducing assembly speed, using coarse threads, avoiding cut bolt threads, mixing nut and bolt grades, and proper alignment are key strategies to prevent galling․
4․1 Lubrication of Threads
Lubrication is a critical preventive measure against thread galling․ Applying lubricants to both internal and external threads reduces friction and heat generation during assembly․ This minimizes the risk of metal-to-metal contact, which is a primary cause of galling․ Suitable lubricants include oils, greases, or specialized thread compounds․ Regular lubrication ensures smooth interaction between threads, preventing wear and tear․ It also facilitates easier disassembly by reducing the likelihood of threads seizing․ Proper lubrication not only extends the lifespan of components but also enhances overall assembly efficiency and reliability across various industrial applications․
4;2 Reducing Assembly Speed
Reducing assembly speed is an effective method to minimize the risk of thread galling․ High-speed power tools can generate excessive friction and heat, increasing the likelihood of galling․ Slowing down the assembly process allows for better control over the torque and tension applied to the threads․ This approach prevents sudden surges in friction that can damage the threads․ Additionally, using hand tools or torque-controlled wrenches can help maintain a consistent and safe assembly speed․ By slowing down, the likelihood of galling is significantly reduced, ensuring smoother and more reliable connections․
4․3 Using Coarse Threads
Using coarse threads is a practical solution to mitigate thread galling․ Coarse threads have a larger pitch and deeper grooves compared to fine threads, which reduces the contact pressure between the nut and bolt․ This lower pressure minimizes the risk of metal-to-metal adhesion and subsequent galling․ Coarse threads also provide a more forgiving assembly process, as they are less susceptible to damage from minor misalignments or debris․ By selecting coarse threads where possible, engineers can enhance the durability and reliability of threaded connections, particularly in applications prone to galling issues․
4․4 Avoiding Cut Bolt Threads
Cut bolt threads are more prone to galling due to their manufacturing process, which can leave sharp edges and stress concentrations․ Unlike rolled threads, cut threads do not work-harden the material, making them less resistant to friction and wear․ This increases the likelihood of metal-to-metal adhesion during assembly․ To minimize galling risks, it is recommended to use bolts with rolled threads, as they have smoother surfaces and higher durability․ Avoiding cut bolt threads in applications where galling is a concern can significantly enhance the reliability and lifespan of threaded connections․
4․5 Mixing Nut and Bolt Grades
Mixing nut and bolt grades with different hardness levels can effectively reduce galling․ When components have similar hardness, they are more likely to seize due to metal-to-metal adhesion․ By pairing a harder bolt with a softer nut, or vice versa, the risk of galling decreases․ This approach ensures that the softer material deforms slightly, creating a more even distribution of the load and reducing friction․ Proper grade mixing maintains mechanical integrity while preventing the abrasive wear associated with thread galling, making it a practical solution in various industrial applications․
4․6 Proper Alignment Techniques
Proper alignment is crucial to prevent thread galling․ Misaligned bolts and nuts can lead to uneven stress distribution, increasing friction and heat during assembly․ Using alignment guides or fixtures ensures that components mate correctly, reducing the risk of metal-to-metal seizure․ Properly aligned threads engage smoothly, minimizing wear and the likelihood of galling․ This technique is especially important in applications involving high torque or repetitive assembly, as it helps maintain thread integrity and extends the lifespan of fasteners․ Correct alignment is a simple yet effective preventive measure against galling․
4․7 Cleaning Threads Regularly
Cleanliness plays a vital role in preventing thread galling․ Dirt, debris, or residue on threads can increase friction during assembly, leading to galling․ Regularly cleaning both internal and external threads ensures smooth engagement and reduces wear․ Use compressed air or solvents to remove contaminants, and avoid reusing dirty fasteners․ Clean threads promote proper lubrication and even load distribution, minimizing the risk of metal seizure․ This simple maintenance practice significantly enhances the reliability and performance of threaded connections across various industrial applications, making it a key preventive measure against galling․
4․8 Controlling Torque and Tension
Controlling torque and tension is critical to prevent thread galling․ Excessive torque can generate heat and friction, increasing the likelihood of metal seizure․ Using torque wrenches ensures precise control, applying the correct force without over-tightening․ Proper tension maintains even stress distribution across threads, reducing galling risks․ Avoid sudden or excessive force during assembly, as it can cause irreversible damage․ By adhering to recommended torque specifications and maintaining controlled force, you minimize wear and ensure reliable connections, safeguarding against galling in both initial assembly and long-term use․
Solving Thread Galling Issues
Thread galling is a common issue during assembly, caused by high pressure and friction․ Effective solutions include lubrication, controlled torque, and proper alignment techniques to minimize damage․
5․1 Applying Lubrication During Disassembly
Lubrication is a critical step in addressing thread galling during disassembly․ Applying a high-quality lubricant reduces friction between the threads, preventing further damage․ This method is especially effective for stainless steel components, as it lowers the risk of seizing․ Regular lubrication not only eases the disassembly process but also protects the threads from wear, ensuring smoother reassembly․ It is recommended to use lubricants specifically designed for threaded connections to maximize their effectiveness and prevent future galling issues․ Proper application ensures components remain intact and functional․
5․2 Using Thread Repair Kits
Thread repair kits are essential for restoring damaged threads caused by galling․ These kits typically include taps, dies, and inserts to recreate smooth, functional threads․ For stainless steel components, specialized inserts are recommended to prevent recurrence․ Proper installation ensures the repaired threads are strong and durable․ Using a thread repair kit not only saves time but also reduces costs by avoiding component replacement․ It is crucial to follow the manufacturer’s instructions for optimal results․ Regular use of such kits can extend the lifespan of threaded components and maintain their performance in various applications․
5․3 Replacing Damaged Components
When thread galling causes severe damage, replacing the affected components is often the only solution․ This is particularly common with stainless steel components like SS316L, where galling can render threads unusable․ Replacing damaged parts ensures system integrity and prevents further complications․ It is crucial to use high-quality replacements that meet original specifications to avoid recurring issues․ Proper installation techniques, such as controlled torque and alignment, are vital to prevent future galling․ Regular maintenance and inspections can help identify and address potential problems before they escalate, reducing the need for costly replacements․
Real-World Applications
Thread galling impacts various industries, including automotive manufacturing, aerospace engineering, marine hardware, and industrial machinery․ These sectors rely heavily on threaded components, making galling prevention crucial․
6․1 Automotive Industry
Thread galling is a significant concern in the automotive industry, where precision and reliability are paramount․ Galling can occur in engine components, bolts, and fasteners, leading to costly repairs and downtime․ Automotive manufacturers often use stainless steel and other corrosion-resistant materials, which are prone to galling due to their hardness․ Preventing galling in vehicle assembly is crucial to ensure safety and performance․ Lubrication and proper torque control are essential strategies to mitigate this issue․ The automotive sector also benefits from using coarse threads and avoiding high-speed assembly tools to reduce friction and heat, which are primary causes of galling․
6․2 Aerospace Engineering
In aerospace engineering, thread galling is a critical issue due to the high-stress environments and the use of materials like stainless steel and titanium alloys․ These materials, while durable, are prone to galling because of their hardness and susceptibility to friction․ The consequences of galling in aerospace can be catastrophic, leading to component failure and potentially endangering entire systems․ To prevent galling, aerospace manufacturers often employ specialized lubricants and precise torque control during assembly․ Proper alignment techniques and the use of thread chasers to ensure smooth surfaces are also essential․ These measures help maintain the integrity and reliability of aerospace components, ensuring both safety and optimal performance in demanding applications․
6․3 Marine Hardware
Thread galling is a significant concern in marine hardware due to the harsh environments and constant exposure to seawater and humidity․ Stainless steel fasteners, commonly used in marine applications, are particularly susceptible to galling because of their hardness and the friction generated during assembly․ Corrosion and wear from saltwater exacerbate the issue, leading to difficult disassembly and potential component failure․ To mitigate galling in marine hardware, manufacturers often use lubricants specifically designed for marine environments and apply coatings to reduce friction․ Regular maintenance, including cleaning and inspecting threads, is also crucial to prevent galling and ensure the longevity of marine equipment․
6․4 Industrial Machinery
Thread galling is a prevalent issue in industrial machinery, where high torque and heavy loads are common․ The repetitive assembly and disassembly of components can lead to increased friction and heat, exacerbating galling․ Stainless steel and other high-strength materials often used in machinery are particularly prone to this problem․ To address galling, manufacturers employ lubricants, slower assembly speeds, and coarse threads․ Regular maintenance, including thread cleaning and inspection, is essential to prevent galling and maintain operational efficiency․ Proper alignment techniques and controlled torque also play a crucial role in mitigating this issue in industrial settings․
Materials and Their Role
Thread galling is influenced by material choices, with stainless steel being prone due to its hardness․ Using materials with varying hardness levels and coatings that reduce friction can help mitigate galling issues․
7․1 Stainless Steel Components
Stainless steel, particularly SS316L, is highly susceptible to thread galling due to its high hardness and tendency to cold weld․ When assembling components made of similar grades, friction and heat generated during tightening can cause micro-welding between threads․ This leads to severe galling, making disassembly difficult and potentially damaging the components․ To combat this, it is essential to use appropriate lubricants, reduce assembly speed, and consider alternative materials or coatings․ Mixing nut and bolt grades can also help mitigate galling issues in stainless steel applications․
7․2 Titanium and Other Alloys
Titanium and other high-strength alloys are prone to thread galling due to their unique material properties․ Titanium’s high strength-to-weight ratio and corrosion resistance make it ideal for aerospace and medical applications, but its softness compared to stainless steel increases galling risks․ When titanium components are assembled, friction and heat can cause microscopic embedding of particles, leading to severe galling․ To mitigate this, lubrication is crucial, and using coarse threads can reduce contact pressure․ Mixing titanium with bolts of different materials or grades can also help prevent galling, ensuring reliable performance in critical applications․
7․3 Coated Materials
Coated materials play a significant role in preventing thread galling by reducing friction and enhancing surface durability․ Coatings such as chromium, nickel, or ceramic act as a barrier between metal surfaces, minimizing direct contact and the risk of particle embedding․ Properly applied coatings can significantly lower the likelihood of galling, especially in high-stress environments․ However, the coating process must be carefully controlled to ensure even layers and avoid uneven surfaces, which could exacerbate galling․ Regular inspection and maintenance of coated threads are essential to sustain their protective benefits and prevent wear over time․
Tools and Techniques
Thread chasers and taps are essential tools for maintaining thread quality, while torque wrenches ensure precise control during assembly, helping to prevent galling issues effectively․
8․1 Thread Chasers and Taps
Thread chasers and taps are vital tools for maintaining thread integrity and preventing galling․ Chasers are used to clean and restore damaged or worn threads, ensuring smooth surfaces․ Taps, on the other hand, are employed to cut new threads in materials, providing precise alignment and finish․ Together, these tools help eliminate surface irregularities and ensure proper thread engagement, reducing friction and the risk of galling․ Regular use of chasers and taps, especially in materials like stainless steel, is essential for maintaining the longevity and performance of threaded components in mechanical systems․
8․2 Torque Wrenches and Control
Torque wrenches play a critical role in preventing thread galling by ensuring precise control over the tightening process․ Excessive torque can generate high friction and heat, leading to galling․ Using torque wrenches allows for accurate application of recommended torque values, minimizing these risks․ Proper calibration and maintenance of torque tools are essential to ensure reliability․ Additionally, controlling torque during both assembly and disassembly helps preserve thread integrity and prevents damage to fasteners, making torque control a key preventive measure against galling in various industrial applications․
Quality Control and Testing
Quality control involves regular inspections of threaded components to detect early signs of galling․ Testing includes visual checks and adherence to industry standards, ensuring threads meet specified tolerances and surface finishes to prevent galling․
9․1 Inspection Methods
Inspecting threaded components for galling involves visual checks for wear, scoring, or seizure․ Dimensional measurements ensure thread accuracy․ Surface roughness testing detects imperfections․ Lubrication presence is verified, and torque tests assess assembly difficulty․ Microscopic examinations reveal early galling signs․ These methods help identify issues before they escalate, ensuring reliability and safety in critical applications․
9․2 Testing Standards and Specifications
Testing standards for thread galling involve precise measurements and evaluations to ensure compliance with industry specifications․ Organizations like ASTM and ISO provide guidelines for thread dimensions, surface finish, and lubrication requirements․ These standards help verify that components meet quality benchmarks, reducing galling risks․ Regular testing ensures consistency in production, while specifications outline acceptable tolerances for thread geometry and material properties․ Adherence to these standards is crucial for maintaining reliability and performance in threaded connections across various industries․
Industry Standards and Best Practices
Industry standards and best practices are crucial for minimizing thread galling․ Following ASTM and ISO guidelines ensures proper thread dimensions and surface finishes․ Adhering to manufacturer recommendations, using appropriate materials, and applying consistent lubrication practices help maintain reliability and performance in threaded connections․
10․1 Following Manufacturer Guidelines
Following manufacturer guidelines is essential for preventing thread galling․ Adhering to recommended torque specifications, material pairings, and lubrication practices ensures compatibility and reduces friction․ Proper thread engagement and surface finishes, as specified by manufacturers, minimize wear and tear․ Using approved tools and assembly techniques further mitigates galling risks․ Compliance with these guidelines not only extends the lifespan of components but also ensures reliable performance in critical applications․ Always consult the manufacturer’s documentation for specific recommendations tailored to the materials and conditions involved․
10․2 Adhering to International Standards
Adhering to international standards is crucial for minimizing thread galling risks․ Standards like ISO and ASTM provide guidelines for thread design, material selection, and assembly practices․ These specifications ensure compatibility between components and reduce friction․ Compliance with these standards enhances the reliability and safety of threaded connections․ By following established protocols for torque limits, lubrication, and surface finishes, industries can significantly reduce galling occurrences․ International standards also promote consistency across manufacturers, ensuring optimal performance and longevity of fasteners in diverse applications․
Future Trends
Future trends focus on advancing material science and tool technology to reduce thread galling․ Innovations in coatings and surface treatments aim to enhance durability and resistance․
11․1 Advances in Material Science
Advances in material science are pivotal in mitigating thread galling․ Researchers are developing new alloys and coatings with enhanced tribological properties, reducing friction and wear․ These innovations include ultra-hard surface treatments and self-lubricating materials, which significantly lower the risk of galling․ Additionally, the use of advanced composite materials is being explored to create threads that are inherently resistant to galling․ Such developments promise to revolutionize industries by improving the reliability and longevity of threaded connections, minimizing maintenance, and enhancing overall performance across various applications․
11․2 Innovations in Tool Technology
Innovations in tool technology are transforming the prevention and management of thread galling․ Advanced tools now incorporate features like automatic lubrication systems and precision thread-cutting mechanisms, ensuring smoother surfaces and reduced friction․ Additionally, tools equipped with sensors monitor torque and tension in real-time, preventing excessive force that can lead to galling․ Laser-cutting tools are also being developed to create threads with optimal surface finishes, minimizing wear․ These technological advancements not only enhance the manufacturing process but also reduce the likelihood of galling during assembly and disassembly, improving overall efficiency and component reliability․